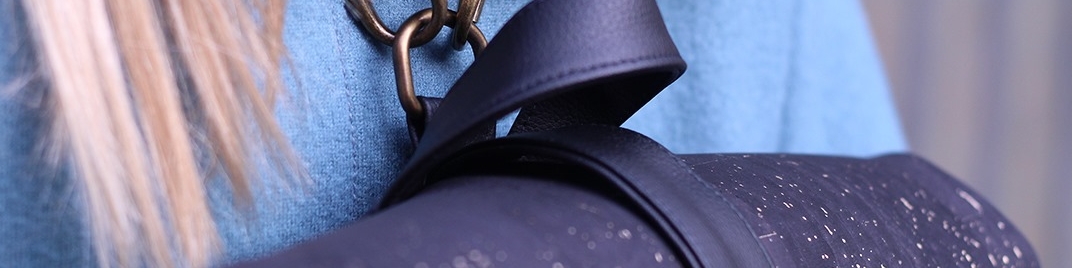
Cactus leather is a natural, sustainable and easy-to-grow alternative to traditional leather. It has excellent technical characteristics - resistance and durability, flexibility, softness, feel and texture like real leather. It is a eco friendly material that is partially biodegradable. It is a sustainable material made from the Opuntia Cacti, also known as Nopal. The inventors of this innovative product are Adrián López Velarde and Marte Cázarez who founded Desserto in Mexico.
To produce Desserto Cactus Leather, the main raw material, cactus, is grown to maturity after which the fully-grown leaves are harvested without causing any damage to the actual plant. This means that a new harvest is produced every 6-8 months. The cactus is grown with rainwater and no artificial fertilizers are added because of the nutrient-rich soil of Zacatecas in Mexico.
The best Nopal leaves are selected for their resilience and strength. Because of their inherent ability to handle extreme temperatures, the leaves can handle low temperatures during the cold months. One of the best parts about using cactus as a raw material is that the plantation is perennial. This means that their plantation lasts for a cycle of 8 years!
After harvesting, the leaves are dried under the sun for a couple of days to achieve desired humidity levels. This organic material is then processed via a patented formulate to create Desserto. The leftover organic material that is not used in the production process is exported and sold in the food industry.
Cork leather is made from the bark of Cork Oaks tree. Cork Oaks grow naturally in the Mediterranean region of Europe, which produces 80% of the world’s cork.
Cork trees must be at least 25 years old before the bark can be harvested and even then, the harvest can only take place once every 9 years. When done by an expert, harvesting the cork from a Cork Oak does not harm the tree, on the contrary, the removal of sections of the bark stimulates regeneration which extends the life of a tree. A cork oak will produce cork for between two to five hundred years. The cork is hand cut from the tree in planks, dried for six months, boiled in water, flattened and pressed into sheets. A fabric backing is then pressed on the cork sheet, which is bonded by suberin, a naturally occurring adhesive present in the cork.
Cork leather is strong but has a smooth and shiny finish. It is water, flame, scratches, stains resistant and hypoallergenic. Fifty per cent of the volume of cork is air and consequently products made from cork leather are light.
The material was developed by Frumat and is made by Mabel, an Italian manufacturer. Relatively new, the material, which is officially named Apple Skin, was first made into bags in 2019.
Apple leather is a bio-based material, meaning that it is partly biological: natural, organic. In the Tyrol region of northern Italy, an enormous amount of apples are grown. These apples are pulverised into delicious juice, and made into jams. When making juice or jam, the seeds, stalks and skins of apples can’t be used. Before apple leather came to be, these ‘left-overs’ were simply discarded, unuseable by the industry.
Today, Frumat collects these otherwise wasted fruit scraps and turns them into a fashionable material. The left-overs, like the apples turned to juice, are crushed, and then naturally dried into a fine powder. This powder is blended with a kind of resin that is, essentially, dried and laid flat into a final material -- apple leather.
Up to 50% of the final material is apples, and the remaining material is the resin, which basically coats and holds together the powder. This resin is what makes up conventional synthetic leather, and it’s called polyurethane.